The Dairy Supply Chain: From Farm to Fridge
By Karen M. Kroll
Tags: Legislation, Public Policy, and Regulations, Temperature-Sensitive Goods, E-commerce, Food Logistics, Specialized Logistics, Transportation, Logistics, Technology , Supply Chain
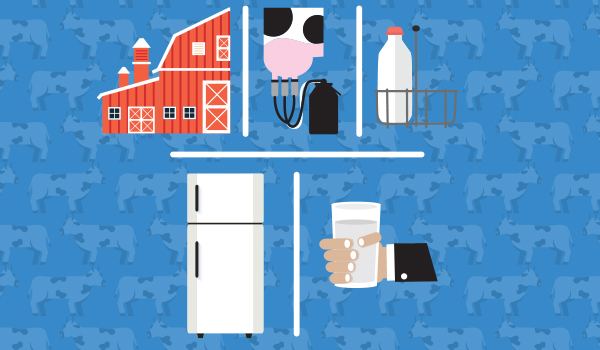
How milk and other dairy products moo-ve from tens of thousands of cows to store shelves across the country — with udder efficiency.
Ron Hurlimann has been a dairy farmer for nearly all his 62 years. Even though he can sense when a cow isn't feeling well, Hurlimann recently affixed radio-frequency identification (RFID) tags to the 100 head of cattle on the dairy farm that he owns and operates on the Oregon coast. The RFID tags track when a cow is eating or resting, as well as its health. Low activity or a cold body temperature can signal that a cow isn't feeling well, while a spike in activity can mean a cow is in heat.Many dairy farmers, processors, and distributors employ technology to automate tasks previously done manually. Automation not only streamlines the work, but it often allows farmers to produce more and better products, and to continually monitor the health of their herds. It also helps those products move from farms to consumers' tables more quickly and with greater visibility.
Hurlimann's total investment for tags, sensors, and a laptop totalled approximately $14,000. But, that investment has been worth it. "The technology is a huge plus," Hurlimann says. "I can tell if cows are sick without scrutinizing them." Even experienced dairy farmers can overlook a cow whose behavior has undergone a slight change, he notes.
These technological capabilities are increasingly critical as the dairy supply chain grows more complex. One reason for the complexity is the proliferation of new dairy products, such as lactose-free milk, organic and Greek yogurt, and single-serve packages of ice cream.
Another reason for supply chain complexity is legislative. While dairy products have always been subject to temperature and cleanliness testing, the requirements are likely to become even more stringent when additional provisions within the Food Safety Modernization Act, which became law in 2011, go into effect. One example is the March 31, 2016, deadline for the final regulations related to the sanitary transportation of food. "Storage and shipping requirements will grow more rigorous," says Bryan Whitmore, director of business development for Ryder Systems, a third-party logistics provider based in Miami, Fla.
An efficient, effective supply chain is increasingly key to success within the dairy industry. "Time, temperature, humidity, cost, distance, demand, forecasting, and packaging are all important considerations in developing a strong dairy supply chain," says Josh Thomas, senior director of communications for the Oregon Dairy Products Commission.
HOW NOW DAIRY COW?
The dairy supply chain starts on one of the approximately 50,000 dairy farms in the United States. Milk typically moves from the cows via pipes connected to cooling storage tanks, also located on the farm. "That is where the cold chain begins," says Thomas. Milk remains in the storage tanks, where it's kept at below 40 degrees Fahrenheit for no more than 48 hours.
Tanker trucks pick up and transport the milk to a dairy processor, where it's tested to ensure it has been properly chilled, and is free of bacteria. Any milk that fails is discarded. "Milk is one of the most tested food and beverage products," Thomas notes.
At the processor, milk is homogenized, pasteurized, packaged, and shipped to retailers in refrigerated trucks. It often is on store shelves within two days after it leaves the farm, although some milk products, such as cheeses, take longer.
Ensuring that milk moves rapidly from farm to store shelf is a complicated undertaking. Despite some recent consolidation, the dairy industry remains largely fragmented. In 2012, only 1,800 farms had at least 1,000 cows, according to the U.S. Department of Agriculture.
Even though milk poses a high risk of expiration and spoilage, it usually moves by truck rather than faster and more expensive transportation modes because of its weight. As a result, "supply chains need resilience to eliminate transportation and storage disruptions," says Elliot Rabinovich, a supply chain management professor at Arizona State University.
In fact, the goal is to ensure the milk doesn't remain in one place. "It's critical to be moving the product at all times," notes Will Salter, chief executive officer and president of Paragon Software Systems, a routing and scheduling software provider with U.S. offices in Frisco, Texas.
The current 80,000-pound weight limit for trucks can also be problematic, given the growth in some farms and processing plants. "Outdated federal transportation rules force trucks to leave plants when they are less than full because the trucks reach the current weight limit before they meet their capacity limit," says Chelsee Woodey, director of political programs for the International Dairy Foods Association.
Another challenge is simply the fact that dairy cows can't be turned on and off like machines. While most dairy cow production naturally jumps about 10 to 15 percent in the spring, dairy consumption doesn't automatically follow. "It's a balancing act," says Charles Nicholson, clinical associate professor in the department of supply chain and information systems at Penn State University. "Dairy farms need to have production to handle the peak months, but then they have unused capacity during other months."
THERE'S GOT TO BE A BETTER WHEY
The many ways in which milk can be processed—into cheese, yogurt, and cream, to name a few—also increase supply chain complexity. For instance, whey, a byproduct of making cheese, used to be flushed away or used as animal feed. Now, it's often processed for use in infant formula, snack foods, and body-building products, among other items. While this offers an opportunity for additional revenue, the whey processing may occur at a different plant than the one making the cheese. That adds steps to the supply chain.
It's a similar situation with the proliferation of customized packaging options, such as four-packs of yogurt in which each carton is a different flavor, as well as the growing interest in specialty products, such as lactose-free or organic milk. "It creates SKU proliferation," says Whitmore.
Technology plays an increasing role in helping dairy supply chain partners meet the challenges they face. It often starts on the farm, with what the Midwest Dairy Association calls "precision dairy farming." This term refers to the use of technology to measure physiological, behavioral, and production indicators on individual animals. The goals include maximizing animal performance, early detection of health problems or disease in individual cows and the herd, identifying production problems, and minimizing the use of medication through preventive health measures, according to the association.
One example of precision dairy farming is the robotic milking machine. Cows enter the milking parlor and a laser detects their udders. An arm of the robot attaches to the udders and begins milking. While the milking is underway, the system watches for impurities or other problems.
These machines offer several compelling benefits. First, farmers can milk the cows when they want, rather than adhering to a schedule, says Tim Richards, chair of agribusiness and resource management at Arizona State University. "This is better for the cows," he adds.
Second, milking machines reduce the farmer's workload. That can be key, given the difficulty some farmers face finding workers interested in milking, Hurlimann says.
However, the technology's price tag—often low to mid-six figures—can put it out of reach for many farmers, Hurlimann notes.
Another technology tool is feed and milking management software that tracks the cows' diet and milk production, among other information, Nicholson says. For instance, a farmer can receive reports on a cow's somatic cell count, which indicates the quality of the milk and the health of the animal.
Some larger farms use technology to eliminate one step in the traditional supply chain. Rather than moving milk from cows to a refrigerated storage tank, from which it's pumped into a trailer to head to the processor, milk is pumped from the milking machines directly into a trailer. Drivers hauling the milk leave an empty trailer with the farmers, and attach the full trailer to their rigs. This can cut driver waiting time and reduce the need for on-farm storage. "It typically makes sense for farms with at least 1,000 cows," Nicholson says.
Some farmers use RFID tags and GPS software to keep tabs on their cows' location. An even newer solution is the use of drones to monitor larger herds and farms.
HERD IT THROUGH THE GRAPEVINE
The price tags of many technical tools available to dairy farmers is one reason why the average farm is growing in size. The midpoint herd size—half of all cows are in herds smaller than the midpoint, and half are in herds that are larger—jumped from 101 in 1992 to 900 in 2012, according to the U.S. Department of Agriculture.
Similarly, economies of scale prompted the aggregation of small processing plants in the 1990s. "Improvements in technology are scale-intensive," says Richards. "Dairy farms have to be big to take advantage of the available hardware and software."
Some different solutions come into play once milk leaves the farm. One potential remedy is legislative. In September 2015, Representative Reid Ribble (R-WI 8th District)proposed the Safe, Flexible and Efficient (SAFE) Trucking Act, or HR 3488, which would allow states to set weight limits of up to 91,000 pounds, although trucks would be required to have a sixth axle.
Raising the weight limit would mean fewer trucks on the road. Europe and Canada already allow trucks weighing more than 100,000 pounds, according to information provided by Ribble.
Routing and scheduling software optimizes the time required to move milk from farms to processing plants. The solutions can determine the most efficient route, and help ensure the trucks sent to each farm are the right size. "Farmers don't want to waste milk by not being able to transport it because the truck is too small," Salter says. At the same time, sending trucks that are larger than needed, and travel half-full, wastes money.
When it comes to transporting products to retailers, most processors try to time their deliveries for early in the day so products can move right onto the shelves and in customers' view. Processors enter the agreed-to delivery time with the store into the software, and the routing software accommodates it.
On the flip side, a supermarket may use software to track trucks on their way, so employees are available to receive, unload, and store dairy and other temperature-sensitive products, Salter says. The transportation department can also let individual stores know of any delays or early deliveries by phone, email, or text.
Another shift is a greater demand for sales visibility between wholesalers or distributors, and processors or manufacturers. "The information provided back upstream allows the processor to see which products are selling fast or slow," says Derek Curtis, vice president with HighJump Software, a Minneapolis-based supply chain software provider. "The sales data drives production and tactical decisions, as well as marketing and strategic directions."
Another area of change is the growing use of handheld devices by truckers working within the dairy supply chain. While larger dairies have been using mobile technology to help truckers on the road stay abreast of pricing changes or upcoming promotions, and to track their trucks' locations, the technology is becoming affordable for firms of all sizes. "Carriers no longer need client-server technology and big hardware," Curtis says. "A carrier with 10 trucks can now afford it."
In addition to boosting efficiency, the handheld devices can cut shrinkage. "They provide asset accountability and inventory accountability," Curtis says.
For most milk products, trucking is the only viable transportation mode, given the need to quickly and inexpensively move products to retailers and restaurants. But some companies producing dairy products with longer expiration dates, such as some shredded cheese products, are exploring rail transportation. First, of course, they need to get the product into "shelf-stable form," Nicholson says. They also need to conduct cost-benefit analyses to determine which markets they can best serve this way.
The generally regional nature of the milk supply chains within the United States—given the cost of transportation, it rarely makes sense to ship liquid milk across the country—can present challenges when milk production climbs. Yet, the pounds of milk produced per cow increased from about 17,186 in 1998 to 22,258 in 2014, according to the U.S. Department of Agriculture.
"For instance, the nearly 68 million people in the Midwest are going to drink only so much milk," says David Closs, chair of the department of supply chain management at Michigan State University. "This is where the supply chain part really comes in."
One option is to ship dry milk—essentially milk in which most of the moisture has evaporated—longer distances, and even outside the country. According to the USDA, exports of dairy products reached about $7 billion in 2013. Most of the growth was in dry manufactured dairy products.
This is one example of how the dairy supply chain is changing along with the market. It also highlights the need for strong supply chains. Given the number of variables to balance—inbound and outbound costs, increasing SKU counts, regulations, and rapid product expirations, to name a few—efficiency and visibility are critical. "It's easy to move into the red quickly because there are so many angles to manage," Curtis says.
Relay Races to Optimize its Supply Chain
Visitors to online grocer Relay Foods' website see colorful pictures of organic dairy products, produce, and artisanal cheeses, and read engaging profiles of some of the company's farmer partners. What they probably won't notice is Relay's mastery of logistics and commitment to an efficient, effective supply chain.
"We put a lot of thought into our logistics operation," says Kevin Kurzendoerfer, chief operating officer for the Charlottesville, Va.-based company. "It's one reason we're ahead of other players in the online grocery sector."
For instance, when customers place orders for milk, they receive products with at least five days of use remaining. "We are constantly turning the milk; it's built into our inventory management system," Kurzendoerfer says.
Relay currently serves 12 markets in the Washington, D.C. area. It partners with about 50 farms and 200 artisan producers, and offers more than 8,000 products, with a focus on healthy, local, and organic foods. The company offers two delivery options: It delivers food to about 140 "pick-up" locations where customers get their orders; or it delivers directly to customer homes for a monthly fee.
Learning From Leaders
Efficient fulfillment and logistics strategies are critical to the company's success. To launch these strategies, the management team studied other online grocers to learn what they were doing, and how to adopt or adapt those best practices for their market. They then built information systems platforms to track products and serve customers from end-to-end. "We track products from the minute they come into our facility until they're with a customer," Kurzendoerfer says. "That has enabled us to maintain full data integrity."
For instance, Relay tests dairy products for temperature and quality upon receipt, and then holds them in temperature-controlled coolers or freezers. Sensors log the temperature every 30 seconds, and record the information in a database.
Relay's systems platform essentially combines a virtual retail store with a warehouse management system. So, the moment a customer orders, say, a gallon of milk, it's taken from inventory.
Orders placed before midnight are delivered the following day. When delivering products, Relay uses packaging originally designed for sensitive medicines to ensure milk and other refrigerated items remain cool for eight hours. Customers receive a text message stating the time their order was delivered so they know approximately how long the products will keep their temperature.
Thanks to these efforts, Relay has become a significant online grocer in the Mid-Atlantic area. "We've broken our share of eggs and melted our share of ice cream along the way," Kurzendoerfer says. "But we have learned from those experiences, and now deliver products in perfect condition."
No comments:
Post a Comment